 |
11.11.16 15:54 |
Пост-релиз конференции «Ароматика 2016». Организатор – CREON Energy |
Ситуация на рынке ароматики РФ продолжает оставаться стабильной, но стабильность эта – с пессимистическим оттенком. Веру в светлое будущее сохраняют лишь поставщики технологий и услуг. В реальности же изменений на рынке практически нет: его игроки с любопытством ждут хотя бы одного реализованного проекта.
Компания CREON Energy 19 октября провела в Москве Десятую международную конференцию «Ароматика 2016». Генеральным информационным спонсором мероприятия стал журнал «Нефть России».
Говоря о ситуации на российском рынке ароматических углеводородов, генеральный директор CREON Energy Санджар Тургунов назвал ее уникальной: «Профицит мощностей соседствует с полной гармонией производства и потребления. В то же время профицита по производству не было, нет и не будет. Доказательство этого – полное отсутствие экспорта. При этом проблемы с реализацией имеющегося потенциала в нашей стране налицо. Новые проекты по выпуску и потреблению ароматики анонсируются ежегодно. Сколько из них реализуются? Считанные единицы. При этом обе стороны находят оправдание своей нерешительности: одни говорят об отсутствии видимого спроса, другие – о нехватке сырья. Перейдет ли теория в практику – предлагаю обсудить».
Открыл конференцию традиционный обзор рынка ароматических углеводородов, представленный Леонидом Кручининым, заместителем директора по маркетингу компании «Импэкснефтехим». По итогам 2015 г. производство параксилола в России составило 319 тыс. т, это на 10% меньше уровня предыдущего года. Внутренним потребителям было отгружено 187 тыс. т, остальное отправлено на экспорт.
За 7 месяцев 2016 г. выпуск продукта достиг 197 тыс. т.
На данный момент, говорит г-н Кручинин, не рассматривается ни одного реального проекта, связанного со значительным ростом производства или потребления параксилола.
Структура российского рынка ортоксилола стабильна, объемы производства меняются только из-за аварий или ремонтов. Как сообщил эксперт, производство в прошлом году достигло 219 тыс. т. Из этого объема на внутренний рынок было отгружено 136 тыс. т, остальное отправлено зарубежным потребителям.
За 7 месяцев 2016 г. выпуск ортоксилола подрос на 8 тыс. т до 139 тыс. т. Докладчик отметил, что в 2016 г., в отличие от предыдущих лет, экспортный паритет стабильно превышает цены внутреннего рынка, однако это не привело к перераспределению объемов в пользу экспорта. По его мнению, единственной причиной этого может быть стратегия продаж производителей, в частности, АНК «Башнефть».
Производство толуола в России по итогам 2015 г. составило 134.6 тыс. т, а уже за 8 месяцев 2016 г. этот показатель достиг 130.5 тыс. т. Такой резкий рост связан с увеличением производства на «Омском НПЗ» который на сегодня стал крупнейшим производителем в РФ.
Леонид Кручинин отметил факт появления первого за последнее время долгосрочного экспортного контракта на толуол, который подписала «Роснефть» под влиянием трудностей со сбытом продукта в зимний период.
Бензол традиционно занимает самую большую долю на рынке ароматических углеводородов РФ. Его производство в 2015 г. (за вычетом повторной переработки) достигло 1.22 млн т, из этого объема на нефтяной пришлось почти 77%, на каменноугольный, соответственно, 23%.
За 8 месяцев текущего года объемы производства составили 797 тыс. т, процентное соотношение каменноугольного и нефтяного бензола осталось прежним.
Потребление за эти периоды практически полностью соответствовало производству (без учета экспорта) – 1.16 млн т в 2015 г. и 758 тыс. т за 8 месяцев года нынешнего. Крупнейшее направление потребления – выпуск этилбензола и стирола, а также капролактама.
«На сегодняшний день есть запас мощностей как по производству бензола, так и по потреблению, - резюмировал Леонид Кручинин. - Есть также сезонный фактор технологического характера - дисбаланс в период ремонтов. До тех пор, пока производство стабильно не превысит потенциальных возможностей по потреблению, концепция ценообразования и поведения игроков на рынке не поменяется».
Что касается рынка Казахстана, то ситуация на нем кардинально не поменялась: импорт из этой страны весьма невелик, а запуск на Атырауском НПЗ риформинга для производства ароматики постоянно откладывается из-за дефицита сырья.
Спрос на бензол определяется в первую очередь за счет потребления его в производстве этилбензола-стирола, капролактама и фенола-ацетона. В России, говорит руководитель отдела аналитики CREON Energy Лола Огрель, фенол получают только кумольным методом, в котором сырьем является бензол и пропилен. Мощности по производству фенола в РФ составляют 237 тыс. т, это существенно меньше показателя 2013 г., когда они достигли 300 тыс. т. Этот спад объясняется аварией на «Омском каучуке» и полной остановкой производства фенола на этом предприятии. Средняя по России степень загрузки в 2014-2015 гг. была более 95%. При этом «Казаньоргсинтез» в последние два года работал с превышением мощностей, а «Уфаоргсинтез» - на пределе возможностей. Незначительный потенциал по увеличению производства есть только у «Новокуйбышевской нефтехимической компании». Дальнейшее развитие рынка фенола в России, подчеркнула эксперт, возможно только при наращивании мощностей.
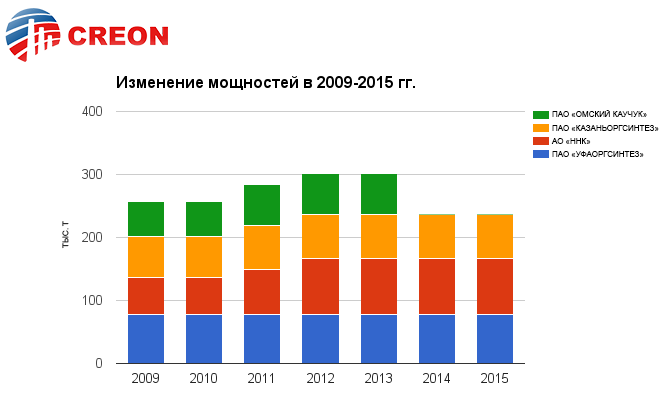
Производство фенола по итогам 2015 г. составило 225.4 тыс. т, это на 6.4% меньше показателя годом ранее. Доли трех оставшихся производителей фенола в общем объеме выпуска сейчас примерно равны.
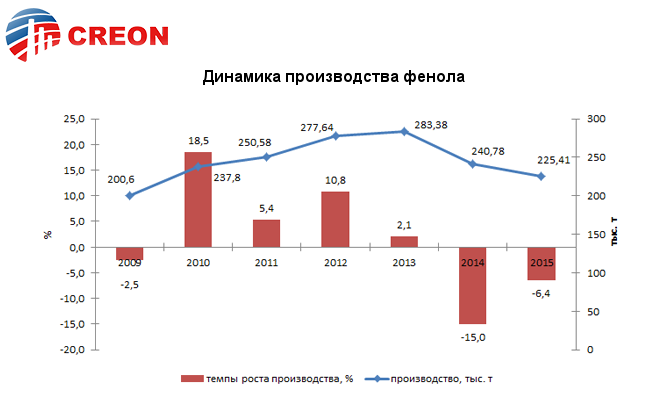
За последние 7 лет объем потребления фенола российскими предприятиями увеличился на 15.4% – с 201 тыс. т в 2009 г. до 232 тыс. т в 2015 г. Среднегодовой темп роста спроса составил 2.2%, однако рынок развивался неоднозначно. И если в 2013 г. можно говорить о сокращении спроса, связанном с экономическим кризисом, то падение 2014 г. – это, несомненно, следствие остановки «Омского каучука» и возникновения дефицита фенола на российском рынке. Положение усугубилось девальвацией рубля и, соответственно, снижением конкурентоспособности импортного фенола. Импорт практически не увеличился, переработчики (прежде всего, «Куйбышевазот») просто решили сократить потребление фенола.
Выпуск фенола в России за 8 месяцев 2016 г. составил 148.6 тыс. т, что на 1% больше соответствующего периода прошлого года. Как сообщила эксперт, потребление при этом сократилось на 0.6%. По предварительным данным, в 2016 г. в целом можно ожидать сохранение показателей производства и спроса примерно на уровне прошлого года, но с измененной структурой потребления. Прогнозируется рост доли ФФС, а также капролактама, это произойдет за счет сокращения доли ДФП (что связано с остановкой производства на «Уфаоргсинтезе»).
Докладчик отметила, что за 8 месяцев по сравнению с аналогичным показателем прошлого года существенно возрос экспорт - с 1.4 тыс. т до 6.5 тыс. т. Отмечено и увеличение объемов импорта.
К 2020 г. , утверждает г-жа Огрель, мощности по производству фенола в России вырастут максимум на 113 тыс. т. В настоящее время рынок стабилен, появление новых потребителей в среднесрочной перспективе не предвидится. Экспорт российского фенола регулируется наличием свободных объемов этого продукта. До запуска новых мощностей не прогнозируются значительные поставки фенола внешним потребителям, а при появлении излишков потенциальным рынком будут страны Восточной Европы.
Основной угрозой для российского рынка фенола является выход дешевого китайского фенола на внешние рынки по мере ввода новых мощностей в Китае, и, как следствие, падение мировых цен на этот продукт.
Дальнейшее развитие рынка фенола возможно только при наращивании мощностей, и один из наиболее перспективных проектов – возобновление производства на «Омском каучуке». ГК «Титан» планирует запустить его в конце 2017 г., сообщил Юрий Жигадло, заместитель генерального директора по МТС ГК «Титан». Цех был остановлен в 2014 г. после аварии, все это время шли восстановительные работы. Сейчас предприятие потребляет 2-3 тыс. т бензола ежемесячно, после запуска эта цифра вырастет, и общее потребление составит до 100 тыс. т/год.
По словам г-на Жигадло, компания ведет переговоры со своими традиционными потребителями фенола, которые закупали продукт до аварии.
В то же время у других игроков рынка проект «Титана» вызывает вопросы. «Сейчас рыночная ситуация по фенолу достаточно сложная, - рассуждает коммерческий директор «КуйбышевАзота» Андрей Былинин. – Восточная Европа не испытывает необходимости в дополнительных объемах. Потенциал рынка по тем ценам, которые хотят получить наши производители, увы, исчерпан. Единственный выход – перерабатывать фенол на месте. Что касается потребности самого «КуйбышевАзота», то в октябре на предприятии введены новые мощности по производству полупродукта – циклогексанона, что позволяет компании выпускать капролактам уже без использования фенола».
Весь капролактам, выпускаемый на Кемеровском «Азоте», - экспортный продукт, говорит главный маркетолог управления «Капролактам» Мария Натарова. Основным потребителем является Китай. Планов по строительству дальнейших переделов компания пока не строит.
«Тезисы, что рынок ароматики в России стабилизировался, и ничего интересного там происходить в ближайшее время не будет, - чистой воды пессимизм, - считает заместитель генерального директора по стратегическому развитию компании «Оргнефтехим Холдинг» Валерий Кузнецов. – Запуск комплекса ароматических углеводородов на «Танеко» изменит расстановку сил на рынке в пользу превышения производства над внутренним спросом». По словам докладчика, первоначальная концепция проекта немного поменялась: сейчас первоочередная задача – закончить строительство риформинга, запустить его и начать получать компоненты топлива. Параллельно будет запущена установка разделения риформата и фракционирования ксилолов мощностью 626 тыс. т/год по сырью. Ориентировочный срок – 2017 г. Фракцию ксилолов, говорит докладчик, компания будет поставлять на рынок и как компонент смешения бензинов, и как компонент нефтехимического сырья. Но все же сначала комплекс будет работать по топливному варианту, причина этого – обеспечить приток наличности на первом этапе работы. Затем, в 2018 г., планируется запуск блока экстрактивной дистилляции Сульфолан ЭД (мощность - 122 тыс. т/год по экстракту). Это станет шагом от производства топлив к выпуску нефтехимической продукции. В 2019 же будут введены в эксплуатацию установки «Парекс», «Изомар», «Таторей», а также установка фракционирования бензола и толуола. Именно этот год Валерий Кузнецов назвал временем «выхода на рынок нефтехимических компонентов»: «Частично мы будет поставлять их на «НКНХ», частично – на внутренний рынок, еще часть пойдет на собственное нефтехимическое производство «Татнефти».
Что касается последующей переработки ароматики, то возможны небольшие задержки в реализации планов. Так, проект по продукции ЛАБ/ЛАБС выведен в «СафПэт», но создание этого предприятия идет медленнее и тяжелее ожидаемого. По словам эксперта, ввод в эксплуатацию состоится в лучшем случае в 2020-2022 гг. К тому же рыночная ситуация диктует свои правила: планируемые изначально бутылочные марки могут быть заменены на волокно.
Генеральной проектной организацией комплекса получения ароматики в Нижнекамске является «Ленгипронефтехим». Как рассказал главный инженер проекта Сергей Шишкин, начиная с момента промышленного освоения процесса каталитического риформинга и по сей день компания является ведущим проектным институтом по данному процессу. Все выполняемые «Ленгипронефтехимом» в последнее время проекты каталитических риформингов реализуются с непрерывной регенерацией катализатора (НРК) как наиболее передовым решением. При этом все они выполняются в составе комбинированных установок, что дает множество преимуществ - компактное размещение, сокращение межустановочных связей, централизованное управление, общие вспомогательные и технологические системы, снижение эксплуатационных затрат до 15% и металлоемкости до 25%, уменьшение количества обслуживающего персонала, снижение стоимости реализации и эксплуатации.
Компания выполняет несколько проектов риформингов с НРК. При этом реализуемые проекты данных установок охватывают все возможные вариации: как по технологии компании «Аксенс», так и по технологиям компании «ЮОПи». Кроме того, выполняются и вариации работы риформингов (как по бензиновому варианту, так и по ароматическому). В ходе доклада детально были изложены основные моменты по проектам комбинированных установок, содержащих в т.ч. секции риформингов с НРК по бензиновому варианту на Туапсинском НПЗ, Киришском НПЗ, Яйском НПЗ.
В проекте «Танеко» компания «Ленгипронефтехим» выступает генеральной проектной организацией по разработке проектной документации в целом по т.н. «бензиновой схеме», т.е. объектам, предназначенным для получения бензинов и индивидуальных ароматических углеводородов. В составе данных объектов спроектирована и строится комбинированная установка, которая представляет собой полный комплекс получения ароматики компании «ЮОПи». Риформинг НРК в составе данной установки работает по ароматическому варианту.
О катализаторах гидрирования и очистки ароматических углеводородов, разработанных совместно CRI и Shell Global Solutions, рассказал коммерческий директор Shell Global Solutions Eastern Europe Сергей Абрамов. По его словам, плохие рабочие условия и/или неправильный выбор катализатора могут привести к высоким потерям ароматики (бензола, толуола, ксилола) и снижению рентабельности (а именно – повышенному потреблению водорода). Решением может стать выбор правильного катализатора: необходим подбор активности катализатора к требованиям системы для достижения потерь ароматики менее 1%. CRI использует собственную кинетическую модель, чтобы определить, какое сочетание катализаторов обеспечит заказчику наилучшие рабочие характеристики, с учетом таких факторов, как срок службы, заданная конверсия и сохранение ароматики. Важным моментом Сергей Абрамов назвал и оптимизацию реактора.
Проблеме разделения этилбензола и стирола был посвящен доклад представителей Sulzer Chemtech – Евгения Николаева и Дениса Чернышева. Колонна разделения «ЭБ/стирол» традиционно требует большого внимания на производстве, потому что с ней связана большая часть потребления энергии на установке, у нее большие размеры, и довольно велик риск полимеризации. Sulzer предлагает оптимизировать процесс очистки стирола, в .т.ч. с помощью использования насадки «МеллапакПлюс».
Докладчики привели пример установки производительностью 200 тыс. т/год. Возможно три варианта модернизации: увеличение производительности с достижением качества, улучшение чистоты стирола добавлением 29 теоретических тарелок либо же максимальное увеличение производительности.
В связи с развитием автомобилестроения и двигателей внутреннего сгорания, вызывающих экологическую опасность, необходим переход на новые энергоносители, не вызывающие такого загрязнения атмосферы, либо же переход на новые технологии производства экологически чистых моторных топлив (ЭМТ). Как рассказала старший сотрудник Объединенного института высоких температур РАН Марина Навалихина, в этой области ведущую роль играют новые катализаторы гидрооблагораживания и особенно нанокатализаторы, способные заменить драгоценные металлы в промышленных катализаторах.
Была проведена многолетняя работа по оптимизации модернизированных Ni-катализаторов и нанокатализаторов в широком круге реакций. Найден способ изменения их активности и селективности путем изменения состава ГПС и расположения активных центров Ni-ГПС в поровом пространстве носителей, поскольку в процессе приготовления создается вторичная пористая структура катализатора. Получены данные по различным физико-химическим методам исследования Ni-нанокатализаторов для гидрирования Ar, олефинов, ароматизации и гидроизомеризации н-парафинов что позволяет использовать эти стадии для гидрооблагораживания синтетического жидкого топлива (ФТ-синтез) и для производства экологически чистого ЭМТ на основе газоконденсатов различного состава.
Все новости индустрии
|
|